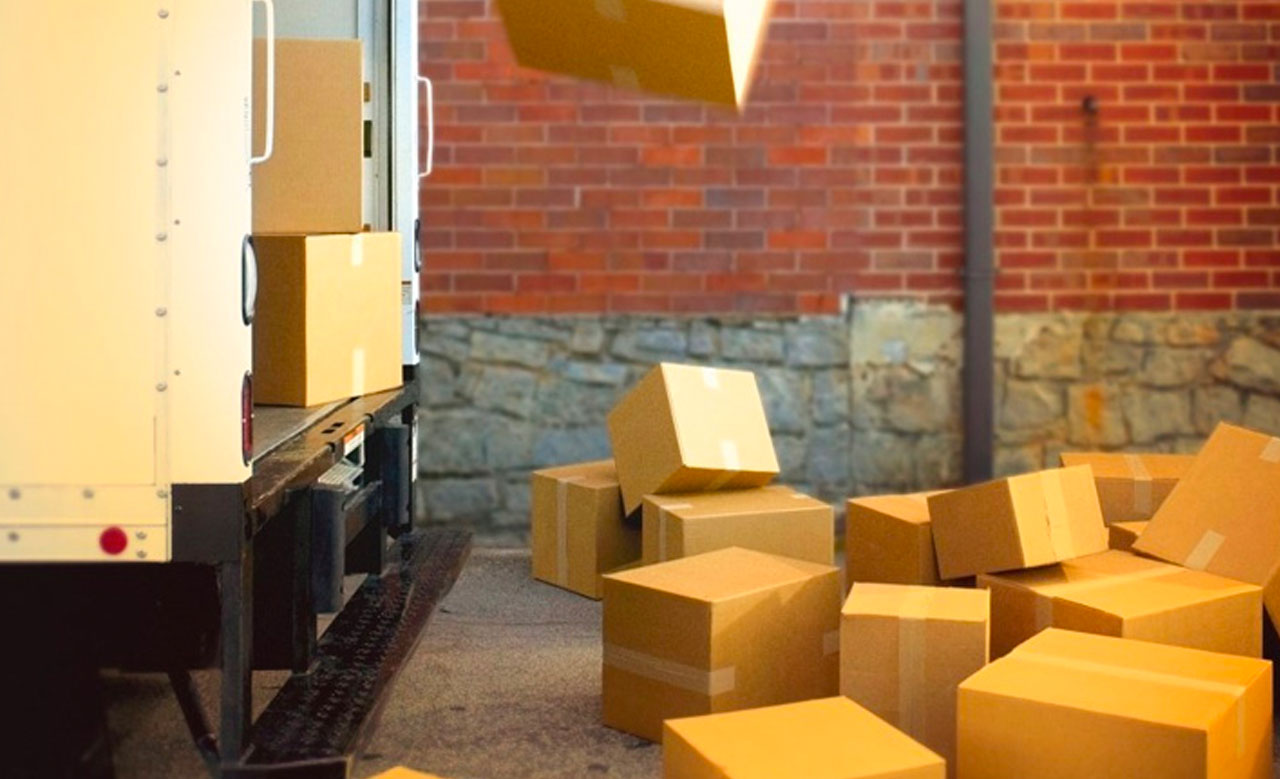
Cushioned package development test method
Optimizing your testing approach is key to understanding and ensuring product durability in real-world conditions.
Lansmont’s Six-Step Method provides a structured, proven approach to package testing, designed to help identify vulnerabilities and enhance product protection.
Follow our guide to develop a more resilient packaging solution and contact us if you need help.
Six step method
for cushioned package development
Product + Package = Environment
Performance packaging is more than an afterthought. Instead, it’s an engineered protective system, designed to make sure that your products arrive without damage, ready to function. So just how much engineering takes place in packaging your products?
Consider this simple formula:
Step 1 - Define the environment
An essential step to designing a cushioned package system is to determine the severity of the environment in which it will be shipped. The general idea is to evaluate the method of distribution to determine the hazards which are present and the levels at which they are present.
These may include such things as accidental drops during handling, vehicle vibration, shock inputs, temperature extremes, humidity levels, and compression loads.
This text will focus on the areas of shock and vibration, but it is important that other areas also receive proper consideration during the package design process. It would be nice to follow every package through the distribution environment and observe what actually happens to it. Usually, however, we must accept another approach. The next best thing to being there is using some sort of recording device to monitor the package and/or the vehicle during shipment. Provided we do this enough times, we begin to gain some sort of statistically valid information which can be used to describe that particular channel of distribution. The events will obviously change from trip to trip, but in general we have an idea of what to expect.
This is the best approach for gaining information about a specific distribution channel. Probably the most widely used approach, however, is to study available published data. The difficulty here is that the data is usually outdated, and was not originally recorded from the environment through which you will actually be shipping your package. In general, however, it may provide the guidelines and rules of thumb necessary for the package design process.
The importance of this environmental information cannot be over stressed. This information will eventually become the part of the package design requirement and if not described correctly the package may appear to fail in distribution even though the design goals were met. In addition, over packaging may result if the actual inputs are lower than those chosen for the design goal.
Step 2 – Define product fragility
Just as the weight of the product can be measured using a scale, the product ruggedness can be measured with dynamic inputs. A shock machine is used to generate a damage boundary curve, and a vibration system is used to map out the natural frequencies of a product.
Shock – Damage boundary
The damage boundary theory is a testing protocol which determines, in an engineering sense, which shock inputs will cause damage to a product and which will not. There are two parts of a shock which can cause damage, the acceleration level and the velocity change. The velocity change, or the area under the acceleration time history of the shock, can be thought of as the energy contained in a shock. The higher the velocity change the higher the energy content. There is a minimum velocity change which must be achieved before damage to the product can occur.
This level is called the critical velocity change. Below the critical velocity change, no damage occurs regardless of the input acceleration level. In essence, there is not enough energy in this region of the damage boundary to cause harm to the product. Exceeding the critical velocity change, however, does not necessarily imply that damage results. If the change in velocity occurs in a manner which administers acceptable doses of acceleration to the product, the velocity change can be very large without causing damage. However, if the critical velocity and the critical acceleration are both exceeded, damage occurs.
Step 3 – Product improvement feedback
This is the time to begin thinking of the product and the package as a product/package system.
Based upon the results of the fragility tests, it may be desirable to strengthen or ruggedize the product rather than ship each one inside an expensive package. Trade-offs between product cost, product reliability, and packaging costs should be identified and ranked for effectiveness. Often times it is possible to raise the fragility level of a product with minor modifications or design changes. This may add a slight cost to each product, but if the packaging requirements drop significantly the total system price goes down.
The ability to get product modifications implemented can vary widely depending upon the atmosphere within each company, and the position of the individual trying to get it accomplished. For some companies, this type of feedback to product designers is a formal step used in developing all new products. This allows the product to become more reliable, of better quality, and also keeps packaging costs to a minimum.
In other situations, particularly when packaging is being developed by an outside supplier, it can be almost impossible to convince a company that making changes to the product is in their own best interest. It is, however, still important to present these ideas and take the role of educator where needed. If possible, try to identify the trade-offs between minor product changes, reliability and repair costs, and packaging expenses.
Step 4 – Cushion material performance evaluation
Material performance data should generally be available from the manufacturer of the material. In certain instances, however, it may be necessary to generate this type of data. This involves examining both the shock absorbing and vibration transmission characteristics of the materials.
It should be noted that the data generated by these methods is applicable to the cushion material only, and may not necessarily be the same as the response obtained in a complete pack. In addition, specimen area, thickness, loading rate and other factors will affect the actual performance of the material in any given situation. What this means is that the data can be used to provide a scientific best guess for the initial package design, but some fine tuning may still need to occur.
Shock cushion performance
A shock cushion curve describes the material in terms of the deceleration transmitted to an object falling on that material at different static loadings. One cushion curve is generated for each material type, material thickness and drop height combination.
The test procedure is basically one of dropping a platen of specified weight from a known drop height onto a cushion of predetermined bearing area and thickness. The deceleration experienced by the platen at impact is monitored and recorded by an accelerometer. Five drops from a particular drop height are performed on a sample at a given static stress loading.
The average of the deceleration readings from the last four of these drops is the value used in plotting each cushion curve point. By adding weights to the platen, the static stress on the cushion material can be changed. Through a series of tests at various static loadings, data is generated and presented in the form of cushion curves (see Figure 10). A minimum of five static loadings are tested to plot each curve, with a new sample being used at each loading
Step 5 – Cushioned package development
The package designer now has all the information necessary to adequately protect the product during distribution. Step 1 defined the types of inputs that the package will receive during shipment.
Step 2 determined the ruggedness of the product and thus its ability to withstand the environmental inputs. Step 3 evaluated the ruggedness to allow for product redesign. Step 4 defined the performance characteristic of packaging materials. Its now time to combine this information into a package design.
Shock – Package design
First, gather together cushion curves for the selected cushion materials. It is important to check that the drop height at which the cushion curves were generated is the same as the design drop height selected in step 1. Next, locate the critical acceleration level determined in step 2 on each of the cushion curves. Draw a horizontal line across the plots through this point. Any portion of the curve which falls below critical acceleration line indicates the static loading range where the material should transmit less than the critical acceleration, see figure 12.
Vibration – Package design
For vibration consideration, we need to collect amplification/attenuation curves for the selected materials. Locate the lowest product natural frequency on each of the curves and draw a horizontal line across the plot. Any portion of the line which extends into the attenuation zone indicates the static loading range where the material should attenuate vibration at the frequencies where the product is most sensitive, see figure 13.
Once the static loadings which appear to provide adequate shock and vibration protection have been identified, material and thickness selections can be made. The actual static loading which is chosen for the package is dependent upon several factors, however designing at the highest possible static loading means using less material. When other considerations such as compressive creep are important, designing at the lowest possible static loading may be warranted. Figure 14 displays the method for calculating the amount of material which must be used around a product to reach a desired static loading.
Step 6 – Test the product/package system
Once the package design is completed, the prototype package system is tested to ensure that all design goals were met.
Shock – Package testing
The package must be able to fall from the design drop height, set in STEP 1, and transmit less than the critical acceleration to the unit. An accelerometer mounted to a rigid portion of the product near the center of gravity can be used to monitor the acceleration level transmitted through the cushioning material into the product. A rigid location is selected so that the input to the product as a whole can be observed during the impact, and thus directly compared to the results of the Step Acceleration test. It may be desirable to monitor additional locations during the tests, such as certain critical components, however the only effective way evaluate package performance is to monitor a rigid location. Packaging itself does not directly change the response of the product to a given input, but it can modify the input which eventually reaches the product.
Flat drops are usually thought to be the most severe drops possible in terms of the acceleration level transmitted to the product. Flat drops focus all of the input along one axis of the unit and little energy is lost to the crushing of corners or edges of the package, or to package rotation. Flat drops, therefore, are used to measure the performance of the package system.
Corner and edge drops, however, often cause damage to the structure of the package which similar flat drops do not. These types of drops are often used as part of a test sequence to verify the package’s ability to hold together during shipment.
Field-to-Lab® Consulting
Lansmont's experienced consulting services team deliver field measurement studies, data analysis, and test specification development.