What is Drop Testing?
Drop testing determines the ability of a package to withstand the impacts prevalent in the distribution environment. This process is vital for ensuring that products travel to customers safely and securely, eventually arriving damage free.
How our drop testing machines help your business
Drop testers help companies save money and maintain positive brand-owner reputations by helping to design packaged products that will deliver products with their intended inherent quality intact. Lansmont Drop Test Systems are the gold standard for accurate and repeatable drop testing. Every drop tester we manufacture is factory-tested to ensure it meets flatness-of-drop requirements and exceeds industry specifications.
You'll find various drop testing machines available at Lansmont that you can choose from based on your individualized needs. Each of our solutions offers different configurations, features and handling capabilities suited for shipments of all shapes and sizes.
Drop Testing Machines in use
Drop Test System Overview
Key components of a drop test system
A drop tester enables product and packaging designers to examine how a product behaves when dropped from different heights, simulating various drop scenarios in a lab environment.
Explore the core components of a Lansmont drop testing system.
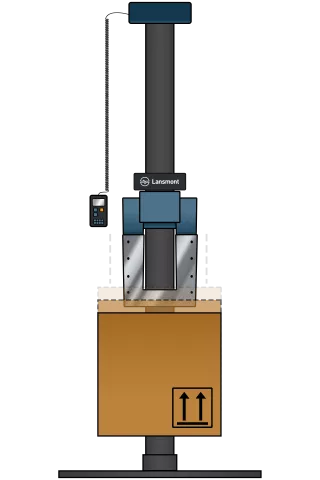
Control system
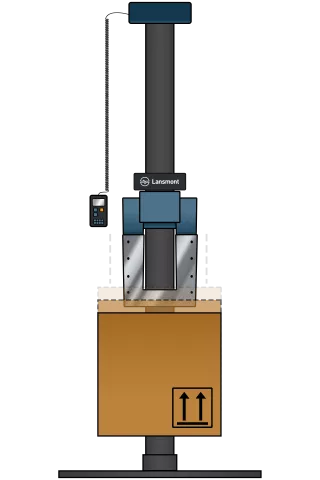
This includes the software and hardware used to configure test parameters, such as drop height and impact force.
You should look for a tester with precise drop mechanisms and accurate measurement instrumentation to ensure reliable results.
Hoist
Mechanical or motorised drop height adjustment
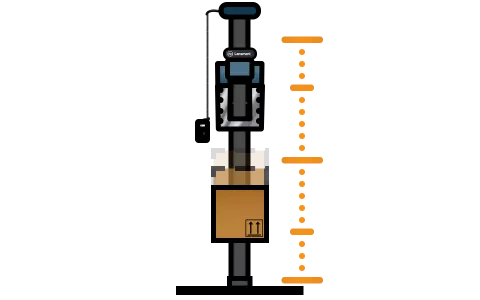
The hoist provides precise drop height adjustment, enabling you to set and adjust the height from which the item will be dropped, allowing for different impact scenarios.
Motorised systems provide greater precision and repeatability, saving time and manual effort.
Controller
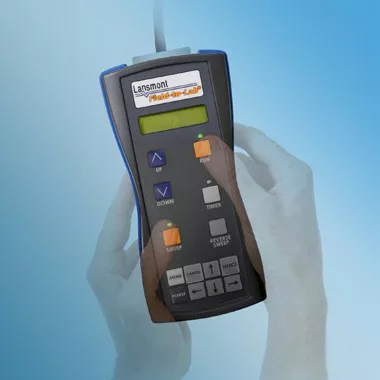
For motorised systems a handheld controller for Lansmont Precision Drop Testers (PDTs) is a plug-and-play device with a straightforward setup and calibration routine.
A digital display simultaneously indicates current and desired drop height settings, with simple controls for setting drop heights.
The controller is lightweight and durable for laboratory environments.
Drop platform
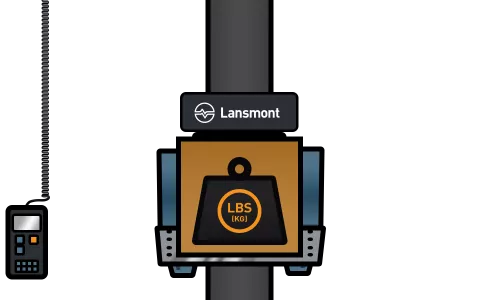
The drop platform, also known as a 'drop leaf', is where the product or package to be tested is placed.
It can be flat or used with specific fixtures to hold the item at varying orientations for different impact scenarios.
When selecting a drop tester it is important to check that the drop platform and tester has an appropriate payload capacity to accommodate your items.
Base plate
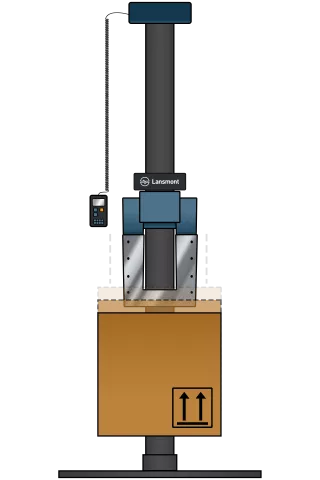
The base platform provides the basic impact surface when drop testing.
Higher capacity (larger payload) drop testers are frequently installed into a recessed floor, making it safer and easier to position unit loads for testing.
Varying fixtures can be used for testing different impact scenarios.
The maximum weight the tester can accommodate should be suitable for the products or packages you intend to test.
Our range of Drop Testers
PDT 80
Precision Drop Tester
PDT 300
Precision Drop Tester
PDT 700
Precision Drop Tester
QR 3000
Quick Release Drop Tester
Customer success with Drop Testers
Investigating last-mile grocery delivery in suburban areas with Lansmont measurement and test equipment
Undergraduates of Virginia Tech have undertaken a compelling investigation into last-mile grocery delivery suburban environments.